Ever wondered what happens when your crankshaft position sensor starts failing? This small yet crucial component plays a big role in your engine’s performance, and ignoring its warning signs could lead to costly repairs. From engine misfires to stalling, knowing the symptoms can save you time and money—keep reading to uncover the seven key signs of a bad crankshaft position sensor.
What Is A Crankshaft Position Sensor?
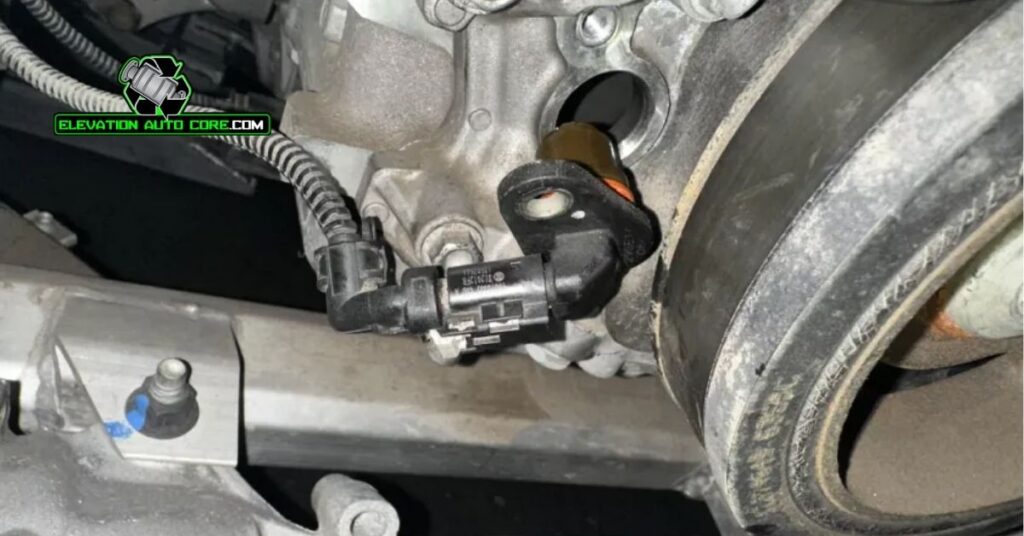
A crankshaft position sensor monitors the rotational speed and position of the crankshaft. It sends vital data to the engine control unit (ECU) for precise fuel injection and ignition timing. Without it, the engine struggles to function efficiently.
Electronic signals generated by this sensor ensure synchronization between engine components. It detects the exact position of piston cycles, helping the ECU optimize performance. Accurate readings are essential to prevent misfires and stalls.
This small component, found near the crankshaft or flywheel, plays a critical role in modern engines. Variations in signal output can disrupt airflow and fuel delivery, leading to performance issues.
Importance Of A Properly Functioning Crankshaft Position Sensor
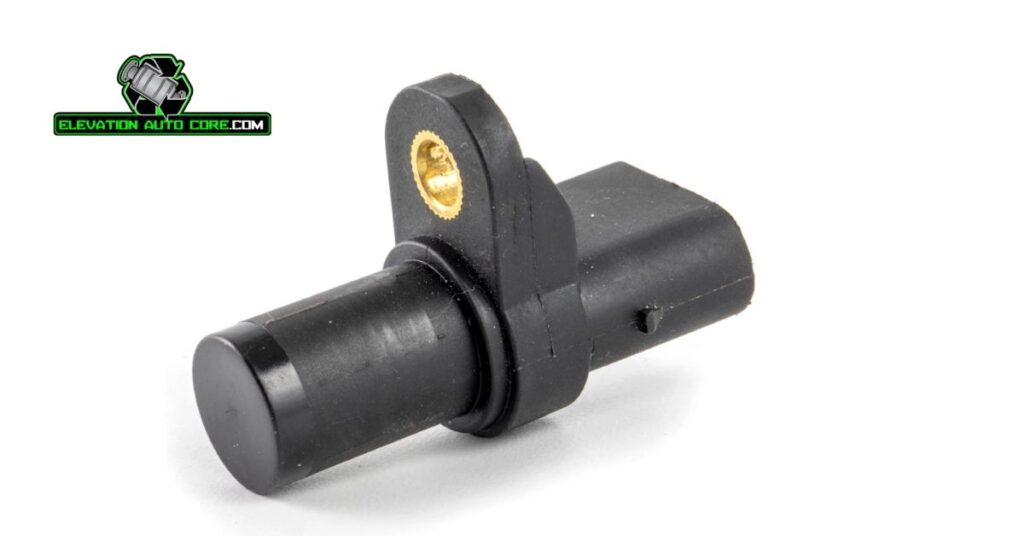
A functioning crankshaft position sensor is essential for engine efficiency. It provides accurate data on crankshaft speed and position to the engine control unit, ensuring proper fuel injection and ignition timing. This synchronization supports smooth operation and maximizes performance.
Interruption in the sensor’s signals disrupts the balance in airflow and fuel delivery. You may experience reduced engine power or inefficient combustion due to this. Continuous sensor functionality prevents these performance losses and costly repairs.
Accurate piston cycle detection optimizes engine timing. Synchronizing components like the valves and pistons promotes consistent functionality. Any deviation in this synchronization negatively impacts both short-term operations and long-term durability.
Detecting early signs of malfunction saves time and repair costs. When the crankshaft position sensor works as intended, engine warnings like misfires or unexpected stalls are avoided.
What Are The 7 Symptoms Of A Bad Crankshaft Position Sensor?
Recognizing the symptoms of a bad crankshaft position sensor helps you address engine issues early. Below are the key signs to watch for.
Engine Stalling Or Misfiring
Stalling can occur unexpectedly when the crankshaft sensor fails to provide accurate data. Misfires might happen due to disrupted ignition timing caused by irregular sensor signals.
Difficulty Starting The Engine
Starting the engine may become inconsistent because the sensor affects the timing for fuel injection. Incomplete data delivery can make it harder for the engine control unit to initiate proper combustion.
Check Engine Light Activation
The check engine light often illuminates when the ECU detects compromised data from the sensor. Fault codes linked to the crankshaft position sensor failure can usually be retrieved during diagnostics.
Poor Fuel Efficiency
Fuel consumption might increase as imprecise sensor input leads to incorrect fuel-air mixture ratios. This inefficiency results from the ECU struggling to maintain proper synchronization.
Engine Vibration Or Rough Idling
Rough idling or engine vibrations might arise if inconsistent signals disrupt the crankshaft’s synchronization. These vibrations often indicate the engine isn’t operating smoothly.
Acceleration Problems
Acceleration may feel sluggish or unresponsive, as the ECU miscalculates fuel injection timing due to sensor defects. This delay impacts the engine’s ability to deliver power.
Ignition Failure
Ignition failure can prevent the engine from starting entirely if the sensor completely stops transmitting data. Without crankshaft position input, the ECU can’t execute ignition sequencing properly.
Common Causes Of A Failing Crankshaft Position Sensor
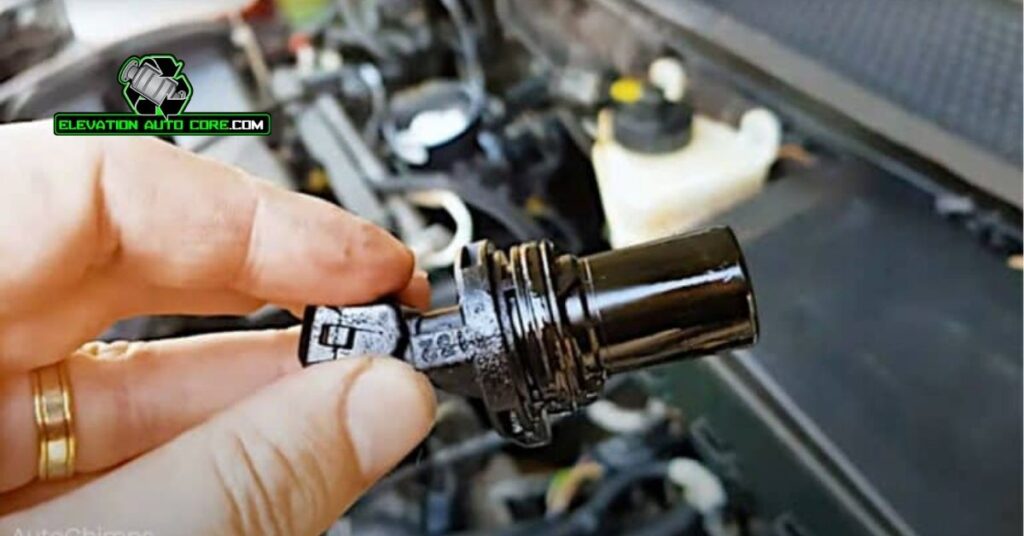
Prolonged exposure to heat can degrade the crankshaft position sensor over time. High temperatures in the engine bay may damage its internal circuitry, leading to inaccurate readings or complete failure. Faulty wiring or electrical connections often disrupt the sensor’s ability to transmit data to the ECU. If wires become corroded, frayed, or loose, signal interruptions occur, impacting engine performance.
Contaminants such as dirt or oil can interfere with the sensor’s functionality. Accumulation of debris may block or impair the sensor’s ability to detect the crankshaft’s position accurately. Aging engines sometimes generate excessive vibration, which may loosen the crankshaft position sensor or misalign it. This mechanical stress can cause intermittent signal issues.
Manufacturing defects also contribute to failure in rare cases. A poorly constructed sensor might have a shorter lifespan and reduced efficiency in data transmission. Damage from engine misfires or sudden stalls can exert strain on the sensor, further diminishing its reliability.
How To Diagnose And Fix A Faulty Crankshaft Position Sensor
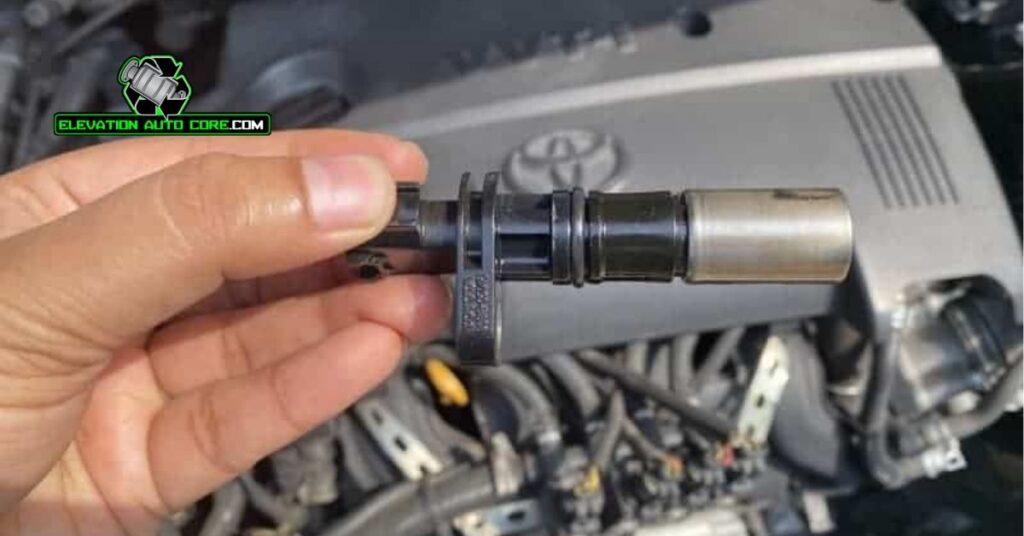
Diagnosing a faulty crankshaft position sensor involves understanding common signs and testing the component accurately. You can start by scanning the vehicle’s onboard diagnostics (OBD) system for error codes, which often indicate sensor issues. Codes like P0335 and P0336 specifically point to crankshaft sensor malfunctions.
Inspect the wiring and connectors for visible damage, loose connections, or corrosion after identifying relevant error codes. A damaged harness can disrupt signal transmission, causing erratic engine behavior. Clean or repair connectors if you detect dirt or corrosion.
Use a multimeter to measure the sensor’s resistance and ensure it’s within the manufacturer’s specifications. Check the service manual for recommended resistance values and perform this test with the ignition off to avoid electrical damage.
Evaluate the sensor’s power supply and ground connections for consistency. Voltage levels between terminals must match the required range specified in your vehicle’s manual. Faulty power supply disrupts the sensor’s performance, leading to incorrect data transmission.
Replace the crankshaft position sensor if testing confirms it’s defective. Disconnect the battery before removing the old sensor to prevent short circuits during installation. Ensure the replacement part matches your vehicle’s specifications for optimal functionality.
Recalibrate the engine’s control unit after sensor replacement. Reprogramming the ECU ensures synchronization with the new sensor, restoring precise fuel injection and ignition timing.
Address underlying issues that caused the sensor’s failure, like overheating or vibrations. Preventing future malfunctions increases the longevity of the new sensor and maintains engine efficiency.
Conclusion
A failing crankshaft position sensor can lead to several engine performance issues that shouldn’t be ignored. Understanding the symptoms and addressing them promptly can save you from costly repairs and prolonged downtime. Regular maintenance and quick action when warning signs appear are essential for keeping your vehicle running smoothly.
By staying proactive and using diagnostic tools like an OBD scanner, you can pinpoint sensor issues early and take the necessary steps to fix them. Ensuring your crankshaft position sensor is in optimal condition helps maintain engine efficiency and enhances your vehicle’s overall reliability.